-
Spare condenser needed
Forum: Air Conditioning
Last Post: johnkosir
07-02-2025, 06:50 PM
» Replies: 5
» Views: 140 -
AC HI/LO on condenser and...
Forum: Air Conditioning
Last Post: pairodice
07-02-2025, 12:04 PM
» Replies: 7
» Views: 316 -
SCS A/C 1301 fan motor sw...
Forum: Air Conditioning
Last Post: whited44
07-02-2025, 10:47 AM
» Replies: 50
» Views: 2,320 -
1990 43' Newell project $...
Forum: Coaches for Sale (Please read the info in the Category description)
Last Post: Jack Houpe
07-02-2025, 02:59 AM
» Replies: 1
» Views: 92 -
New purchase
Forum: Coaches for Sale (Please read the info in the Category description)
Last Post: Lewis and clark
07-02-2025, 02:44 AM
» Replies: 0
» Views: 74 -
A/C resistor for dash AC ...
Forum: Air Conditioning
Last Post: jdkskyking
06-30-2025, 06:11 PM
» Replies: 4
» Views: 664 -
Dash air 2005 - drivers s...
Forum: Air Conditioning
Last Post: jdkskyking
06-30-2025, 04:49 PM
» Replies: 22
» Views: 8,310 -
sewer connection
Forum: Plumbing and fixtures
Last Post: TJ Clark
06-30-2025, 01:00 PM
» Replies: 13
» Views: 18,111 -
Victron Cerbo GX
Forum: Electrical
Last Post: TJ Clark
06-30-2025, 10:01 AM
» Replies: 7
» Views: 300 -
Continue air leaking
Forum: Air Operated Systems and Leaks
Last Post: Jrahn56
06-30-2025, 09:02 AM
» Replies: 2
» Views: 141
- Forum posts:67,873
- Forum threads:8,078
- Members:3,934
- Latest member:Dnfsdd8hFn3
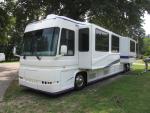
My green travel light has stopped illuminating. I. Verified I am in travel mode by doing the washer sticking to the 4 travel solenoids on six packs.
Leveling system works
I wonder if the light is kaput?
Tom
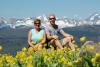
It was my turn to do this. The old radiator had severly corroded fins, and I was starting to notice the engine temps climb. It was running 196 to 205 which is OK but higher than I remembered.
I sourced the radiator and CAC from Atlas in Corpus Christie. I won't bore you with the tight confined work of getting in and out but I did really learn some things on my first go round that may help someone in the future.
Where is the radiator tag? Go to the outside door for the radiator, there is an aluminum trim piece riveted at the left side of the radiator. That trim piece has to be removed to see the tag.
The best thing I did, on day two of the removal by the way, was construct a four foot long two foot wide table and exacly the same height as the engine bay floor. Having that table really gives you somewhere to stand or lay while you shimmy into the bay.
If you remove the bolt in the center of the fan, you can gently tap the fan off the fan motor. It is a taper fit, not a threaded fit. You can't unthread it. Trust me on this one.
The bolts holding the bottom fan shroud to the radiator frame were corroded. Some I could get enough hold on to break the head but two were being ugly. I used a dremel tool with a cut off wheel to gind away the nut from inside the shroud.
Similar thing for the bolts that penetrate the floor holding the fan motor support. I could get an angle grinder in there to cut the bolts off.
Take the bottom shroud off first. And install it last.
I talked to several folks who had done this and they told me the rad/cac comes out bolted together. All I can say is that was NEVER going to happen on my coach without a big cutting torch. So I took them out separately. CAC first, and then slid the radiator out on the aforementioned table.
So obviously it had to go back in in two pieces. CAC first and slide the radiator under it. That's when I discovered that there was not only a gap between the two, but an unevern gap at that. Not wanting to stress the CAC and make it hold the weight of the radiator, I used the unused 1/4-20 holes in the bottom of the radiator frame for jacking screws. By using the screws I was able to lift the radiator the 1/8 inch or so at one end to perfectly fit to the CAC.
Don't even thing about this with one of those radiator hose removal tools. They look like a long pick but the end is hooked so you can get it under the hose and break it loose from the connection. The tool and slightly soapy water also help when putting the hoses back on.
Per Tom's suggestion, I used new silicone hose and new constant tension radiator clamps on the reinstall.
Do replace the flex hose on the exhaust while you're in there. You will never have easier access. I would say mine needed it.
By lifting one end of the radiator at a time onto the table, I made this a one man job. The table is the key.
A forty mile test drive on a 90 degree day showed the temp to go to 196 when the tstats open and quickly drop to 192 so I definitely can see an improvement.
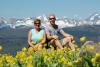
I am posting this so it will be easy to find for someone in a future search.
To make a very long journey short, I have been chasing excessive play or slop in the center of the steering for the last two years.
To that end I adjusted the steering gear sector screw about ten gazillion times, using the TRW recommended method, using trial and error by adjusting at almost every rest stop, using the torque input method outlined in the TRW rebuild manual, and also using a method I made up requiring a dial indicator. I could definitely get it tight, but the play at the center was still there.
So I went on the proverbial witch hunt. I rebuilt the box, but that really wasn't the problem.
I found three things.
One, and most likely the worst offender, was that the pinch bolt which clamps the steering column to the intermediate steering shaft was not tight enough. There was a wee bit of play at that connection. Doesn't seem like much, but that situation is really compounded if you study power transmission. You can have a rotating shaft with two u joints IF, and only IF, both ends are secure. Well one of the ends was not completely secure so that allows a lot more slop than you would imagine. It's easy to access, pull the leather cover off the steering column and it's right at the floor level.
Two, I replaced the universal joints in the intermediate steering shaft. I could feel the slightest lash, and what the heck I had it on the bench while rebuilding the steering box. I looked carefully at the old u joints and the joint races were slightly brinnelled, meaning they were indented. It happens.
Three, and this one is important. For two years I have been looking at the TRW manuals for the steering gear. They all reference a zerk fitting on the output shaft for greasing the output bearing. I NEVER found it, and I looked many times. When I got the box on the bench, it was there plain as day. And, the bearing was DRY. That's not good because it could have been binding the output shaft slightly. Probably wouldn't matter when you steered cause the hydraulics were over power any stiction, but letting the wheels self center could have been impacted if this bearing were tight. So where is this beast. If you are lying on your back looking up at the box. It will be on the side of the box facing the rear of the coach. There is only about two inches of clearance to get your hand up there. It will be at the same level as the output shaft of course. It may have a rubber cover on it so it may not feel like a zerk. There is no way that anyone would ever see this fitting and know to grease it. It is going to take a short right angle fitting on the gun to grease it. If I had any brains I would have installed a remote fitting while I had the box out..
After doing this work and taking a long test drive. I notice two things. One, the dead space in the middle is virtually gone. Two, the steering seems to self center much better without me having to consciously undo the steering input I just made. Or maybe I just know it has to be better after all the work I did
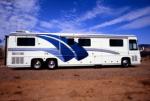
05-03-2017, 08:37 AM
Forum: Coaches for Sale (Please read the info in the Category description)
- Replies (3)
Newell has completed #1622 and it is ready for purchase. http://www.newellcoach.com/newell-coaches/coach-1622/
Quad slide, porcelain flooring throughout, beautiful coach.
I post this solely for your entertainment. Laugh with me, and at me, I deserve it.
I have heard that our strengths are also our weaknesses, and I believe that. I have no fear of anything mechanical and a strong curiosity. I have been taking things apart since I was a baby to see what was inside. Sometimes, though, things may not go back together all that well. And that talent gets me into the very deep end of the pool.
Some of you know about my compulsion with the steering behaviour of the coach. It's ok to snicker about it. I realize it is an obsession. In an effort to improve the freeplay in the center of the steering and reduce side to side wandering, I undertook an effort to carefully quantify exactly where the freeplay in the steering was coming from. I had already measured the slop in all the steering joints using a dial indicator, so I mounted a dial indicator on the end of the pitman arm, and had Rhonda measure how far the steering wheel would move right and left to achieve 0.002 movement at the arm. I was not surprised that it took 1.25 inches at the steering wheel rim to move the pitman arm forward and back 0.002 inches.
All of that nonsense to explain WHY I decided to take the steering gear box out. No matter how tightly the box was adjusted with the sector screw, the freeplay could not be reduced any further. I also could not detect any movement in the universal joints in the steering or the attachment points at either end of the steering shaft.
So off the box comes. By the way, it weighs about 140 lbs. In my younger days, that was an easy bench press. So I am thinking since I am lying on my back directly under it, I should be able to lift it out and lower it. Wrong. Oh I did it. But it pinned me to the ground. I had to roll out from under it.
So off to the bench to see why the gearbox has internal freeplay. By the way, the support engineer at TRW is sick of talking to me. TRW's attitude is that you shouldn't be in that box. It really didn't help my impression of him that his first response to many of my questions was "Why do you need to know that?". Talking about waving a red flag in front of a bull.
Anyhoo, the reason that freeplay is in the box happens to be the way a power steering box works. In short there is a rod in the length of the box. In concept one end of the rod is attached to the steering wheel, the other end attached to the mechanical gears that force the box to work if you lose power steering. In betwixt (that's a redneck technical term you know) there are small ports in the rod that send hydraulic fluid to move the power steering. That rod twists wheel you turn the steering wheel. The twisting opens the ports to activate the power steering, but the rod must twist before anything happens. Well, guess how much it twists. Yep, that is a lot of the freeplay we feel. Gear boxes come with different diameter rods. The small the rod, the more it twists, and the easier the coach is to steer. But the smaller the rod, the more numb the center will be.
The point being I have taken out the gear box and taken it apart only to learn, it's in the design and it's not something that is out of adjustment.
While I have the gearbox out, I might as well put new seals in it. It's not leaking but what the heck. So I wait a week for a seal kit. A hundred bucks or so, but far better than the 1100 Wellman wanted to rebuild it for me. Seal kit comes, I install, and promptly clip the main seal on the hydraulic ram. OOPs, order another seal kit, wait a few days, and try again. That 1100 rebuild is looking better. This time it went together just fine.
Install using ropes pulleys and floor jack. I haven't gotten any stronger and I know I can't just grab it and shove it up there.
Finally, ready to test. Oh by the way, during this same time, I have been replacing the radiator and CAC. While I was in there I retorqued the head, set the valves and jakes, and replaced the flex piece on the exhaust. I am anxious to crank this puppy to see if 1) it will start 2) see if I have leaks 3) and I really want to have the coach mobile for Rhonda's scheduled depart date of May 11. No pressure, right.
It starts and everything is dry. Cool . But I here some weird noise, and I am thinking air in the hydraulic system. After all I had both the hyd fan and the steering box disconnected. I am letting the engine idle and I walk around the coach to get a flashlight. That's when I see a lake of pink foam spewing out of the steering gear like a whacked out Liberace fountain. Holy cow. Kill the engine. By the way, I am having a sinking feeling right about now, and wondering how I was so stupid to ever take this thing apart. I am already imagining two days labor to get it out and put it back in.
The only thing I can imagine is that in my fog I reversed the in and out lines and that has caused this. So I swap the lines and crank up. Wrong, more pink foam. Lot's of pink foam.
Well, I won't post what I said, but it rhymes with yuck. Ok, sit down, have lunch and think about what is wrong. The pink foam is coming out of the vent plug. Hmmm, the only way that can happen is if one particular seal is leaking. I am in luck, there is one piece that you can remove from the box without removing the box from the chassis, and it is the piece with the misbehaving seal. I know I have another seal since, I bought two kits remember?
When I remove the plate, sure enough the seal is displaced and deformed. Ok, take it to the bench and install the new seal. I did, reinstalled the plate, and was fixing to crank again (Yes, fixing to is official Texas terminology). It hit me that the same thing was going to happen. Engineers definition of insanity, doing the same thing but expecting a different outcome. So I removed the plate again.
I have written a novel to get to the goofy part. I took the plate back the bench. Something just didn't seem right about the seal. I remembered removing the old seal and how hard it was to get out, and this one I can press in with my fingers. Nah, 2500 psi is going to blow out anything I can press with my fingers. I have other seals in the kit that fit the shaft diameter perfectly but they are slightly too large to fit into the bore in the plate. The seal I have fits almost perfectly in the bore, but it's just not tight enough. I am thinking one more call to the guy at TRW and ask why the correct seals are not in THEIR rebuild kit. Then the light bulb comes on. When I took out the old seal, I actually tore it apart, and what I think is the bore is part of the original seal. It just so happens that another seal in the kit fits into that bore. Holy cow, batman. Take hammer and chisel and remove the false bore. Bingo, now the other seal will press into place.
Reassemble. Confirm which is the supply line by putting two cups under the disconnected hoses and bumping the engine. The cup that has pink stuff is the supply line.
Woo Hoo, it's dry. We get to go on our trip!
By the way, I replaced the steering universals while I was in there.
But..........the real culprit was that the pinch bolt for the upper connection the steering shaft was not tight enough. When I got the gear box out, it allowed me to feel play between the steering column shaft and the lower steering column.
So all of that for a bolt I could have tightened in five minutes if only I could have detected it.
Sorry for the novel. I hope you didn't strangle on your coffee as you read about my follies.
Safe travels.
I have the 80.3 mm tool that I will gladly loan if you ever need it.
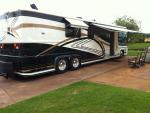
Ron Skeen & my coach at Talladega Speedway for the NASCAR races
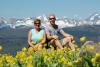
SKF UJ405
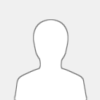
I heard that there was a Newell Rally in Orange Beach, Al this month. I know Newell Plant is not hosting, but wondered if you all knew about it
Cheri
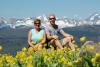
Yesterday I was reinstalling my steering gear box. The details will be posted in a another thread another day.
Its heavy, about 130 lbs, and I was using a combination of a floor jack from below, and ropes and pulleys from above to get it into position.
It slipped and broke one of the air line fittings to the front air bags at the six pack. If I had not cribbed the coach before the work, it could have crushed me before I could get out from under.
It didn't move an inch, although I did have some laundry to do. I must have jerked when it blew because I got a massive leg cramp in my left hamstring. It hurt so I was making some racket. Since Rhonda was manning the jack handle she didn't know what to think for a second.
It's a funny story, but it could have been a tragic one if I had not taken the proper precautions.