-
Temu İNDİRİM KODU [acp856...
Forum: Technology In General
Last Post: Hadio
24 minutes ago
» Replies: 0
» Views: 3 -
Temu Kupon Kodu [acp85670...
Forum: A place where you can post your own or other cool RV Blogs that you follow
Last Post: Hadio
27 minutes ago
» Replies: 0
» Views: 1 -
Temu Türkiye İndirim Kodu...
Forum: Tools
Last Post: Hadio
27 minutes ago
» Replies: 0
» Views: 1 -
Temu Kupon Kodu [acp85670...
Forum: Newell History
Last Post: Hadio
28 minutes ago
» Replies: 0
» Views: 1 -
70% İndirim yada 100€ Tem...
Forum: Members who have hookups and want visitors!
Last Post: Hadio
30 minutes ago
» Replies: 0
» Views: 2 -
What Is The Temu Coupon C...
Forum: Big Rig Friendly places to go
Last Post: Hadio
31 minutes ago
» Replies: 0
» Views: 1 -
Exclusive Temu Coupon [ac...
Forum: Get Togethers
Last Post: Hadio
33 minutes ago
» Replies: 0
» Views: 1 -
$100 Off Temu Coupon Code...
Forum: Full Timing Experiences
Last Post: Hadio
34 minutes ago
» Replies: 0
» Views: 1 -
Latest Temu Coupon Code [...
Forum: Newell Sightings
Last Post: Hadio
35 minutes ago
» Replies: 0
» Views: 1 -
Latest Temu Coupon Code [...
Forum: Newell Sightings
Last Post: Hadio
35 minutes ago
» Replies: 0
» Views: 0
- Forum posts:67,835
- Forum threads:8,085
- Members:3,922
- Latest member:Hadio
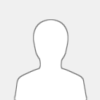
11-10-2024, 10:36 AM
Forum: Coaches for Sale (Please read the info in the Category description)
- Replies (4)
Original owner of a beautiful 1992 coach. Interior is great, marble floor in the kitchen/bath. Coach has been sitting for the last 6 years and needs to be sold. Southern California location and willing to make a great deal. Let me know any questions you might have
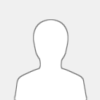
Hello my name is Eliseo new
Owner of a 1991 Newell motorcoach .
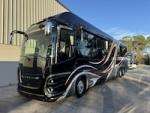
Hello everyone! I’m new to RVing and recently purchased a 2017 P50 model. I have a question about bedding: where might I find or order suitable bedding for my coach aside from going through Newell directly? My model includes two bunks, so I’d like to know if they require special sizing for sheets or bedding. Thank you!
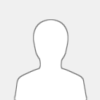
Grohe shower valve
I just made a nice new heavier duty plexiglass cover to cover the rear camera (which was replaced a long time ago!)
Thing is, I am unsure what the original screws were. It has some kind of hex head/slotted sheet metal or wood screws. Is that original?
If so, what size? If Not, what is and what size
Thanks!
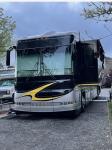
11-05-2024, 08:58 AM
Forum: Coaches for Sale (Please read the info in the Category description)
- Replies (2)
2002, mid entry, three slides coach for sale .$174.k
Good condition with a lot of upgrades, Front saloon remodel with the new sofa and hardwood floor new TV an upgraded ceiling. I bedroom, new carpet, upgraded ceilings on the slide new king size bed, in the bathroom new tile on the floor with new heating mats and new tile in the shower with new faucets. Are all toilets, rebuilt, working flawlessly. I rebuilt Aqua hot system with new improve things with all new elements and new burner new water pump 12 V new air compressor 120 V. All the new Michelin tires with new brakes and new airbags new shocks, new bushings throughout. All new air seals on the slides. New Owning.Coach convert two AMSOIL lubricants throughout and go through service every year, regardless of mileage. , everything in good working condition. Please if you have any questions about the Coach call me 215-834-8720
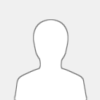
I went out to my coach and the trans stop light is on. Now it won't let me put the coach in drive or reverse. When I parked it everything was good, go out a month later and this happened. Or does anyone know what condition kick the trans stop light on? Any ideas?
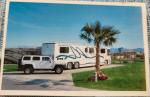
11-02-2024, 11:42 AM
Forum: Coaches for Sale (Please read the info in the Category description)
- Replies (3)
We have owned the coach since 2007. She was originally built for Al Unser Sr. (NASCAR) and then Johnny Rutherford (NASCAR) was the second owner. Stored in Homeland, CA.
Mileage: 139,919 (*see below)
Engine: Detroit Diesel 8V92TA
Fuel: 314 Gallons (separated into 2 tanks). 67 gallons LP
Generator: 12.5 KW Kohler Diesel on front glide out bay
Holding Tanks: 168 Gallons Fresh Water. 173 Gallons Waste Water
Batteries: 2 New House Batteries. 2 New Starting Batteries
Refrigerator: Dometic 3 Way
Extra Ice Maker: Under counter
Outside Freezer: 100 lb capacity access outside bay on pull out tray.
Tool Chest located in outside bay on pull out tray.
Washer/Dryer Combo
2 Carriage Mount A/C’s
Raised roof for headroom
2 TV’s. DVD player and CD Player
Custom Awnings by Zip Dee
Blue Ox Tow Bar for a car or trailer
Rear backup camera
New tires (all 8)
Custom Imron Paint in White with Blue Details
* We originally posted with 39k miles as the title shows 20k as "actual mileage" when we purchased. We were able to get in contact with the dealer that sold us the coach to confirm that the mileage at the time was actually 120k. We put ~19k miles on the coach since purchase in 2007.
Let me know if you have any questions. Thanks!
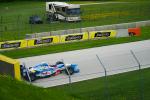
Break Air builds. Can hear the compressor cut off compression release at approximately 130 pis. But no supply side air at the gage. I am not hearing any air leaks.
Had the 120v compressor running with the engine and it never stopped even when the compressor compression release opened. None of the supply side system are operating. Between the 120v not cutting off and the air seat not rising I am guessing it is not just a dash gage issue.
Where do I start trouble shooting?
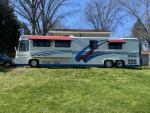
New guy here again. Coach #454. I have an outback inverter in it. It usually shows some time of AC coach load on it when it’s plugged into shore power. My question is why??
Also I went to make coffee this morning and the volt gauge in the inverter went from 13.5 down to the lbco at 12.5 and started charging again.. if it’s on shore power why would it be acting this way??
I’ll include pics of the inverter readout and main gauge panel
I’ve tested the batteries (house and chassis) with the meter and the charger seems to be charging them and the readout at the inverter panel seems to be correct