-
Victron Cerbo GX
Forum: Electrical
Last Post: encantotom
19 minutes ago
» Replies: 3
» Views: 82 -
Continue air leaking
Forum: Air Operated Systems and Leaks
Last Post: HoosierDaddy
1 hour ago
» Replies: 1
» Views: 8 -
Silhouette shades reprogr...
Forum: General
Last Post: Gem930
1 hour ago
» Replies: 0
» Views: 3 -
Dash air 2005 - drivers s...
Forum: Air Conditioning
Last Post: jdkskyking
4 hours ago
» Replies: 9
» Views: 7,746 -
Hunter Douglas mounting b...
Forum: Parts Swap/Giveaway/Sell
Last Post: [email protected]
Yesterday, 05:20 PM
» Replies: 10
» Views: 3,532 -
AC HI/LO on condenser and...
Forum: Air Conditioning
Last Post: HoosierDaddy
Yesterday, 04:58 AM
» Replies: 6
» Views: 149 -
Does anyone recognize thi...
Forum: Howdy and Welcome to Newell Gurus
Last Post: Newell_fox
06-26-2025, 07:25 PM
» Replies: 16
» Views: 837 -
zf transmission problem
Forum: Help, I need help ASAP
Last Post: Andriy Dyachuk
06-26-2025, 01:35 PM
» Replies: 7
» Views: 1,709 -
Front End Upgrade
Forum: Suspension/Tires/Wheels
Last Post: [email protected]
06-26-2025, 05:17 AM
» Replies: 11
» Views: 755 -
Early 90's Coach Settles ...
Forum: Air Operated Systems and Leaks
Last Post: Richard
06-25-2025, 03:44 AM
» Replies: 3
» Views: 152
- Forum posts:67,812
- Forum threads:8,074
- Members:3,919
- Latest member:Hadiji
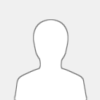
The original Grohe kitchen faucet started leaking from back of the pull-out spray head. I had tried to get it apart to see if we could fix it, but it wasn't coming apart.
We weren't very fond of the white plastic anyway so we took the opportunity and replaced it and the insta-hot faucet.
We found a matching pair of faucets, one for the main and one for the insta-hot on the website perigold.com that we really liked. The brand is Brizo and they make some pretty cool stuff.
Just wanted to share a small update to the coach.
(Please ignore the stained blinds, they're also on the short list for updating lol)
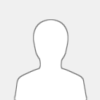
I have a york compressor. Discharge line runns forward but I have not found the condenser/fan. Searched forum but did not find reference.
JD
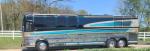
I have heard more horror stories about slides than I want, we all have had problems with the HWH slides and its safeguards which in a way make their product unreliable and expensive to repair besides to say obsolete now. HWH has one hydraulic pump which controls slide locks, raises floors, moves slide in and out all controlled by a brain that must have certain criteria met in order to have valves switch open and close to send fluid to each hydraulic ram one at a time. Many limit switches control this process and the brain hopefully can get the right solenoid open to make the magic happen. Why didn't they use a 12vdc double action hydraulic pump for each hydraulic ram? My count is 3 pumps for a 2 slide coach, 1 for main slide, 1 for floor up and down, and 1 for rear slide. These pumps have a single valve that opens to pump and closes to hold so no need for locking pins as hydraulics does not compress. I would bet the DC amps required to operate these hydraulic rams to me minimum, two pumps could be located where the old unit is and 1 under the bed in the back. Use the existing limit switches to control lights for full in or full out, floor up or floor down up and down and when the light comes on or you hear the pump load quit pressing the switch. The electrical part of the system could be simplified by using just relays, and momentary switches for reversal of the hydraulic pump. You would still have to turn a key to activate the system and bleed the air seals.. Gordon and I briefly talked about something different awhile back and my head has been spinning. Looking forward to feedback on this and I may use our coach as a test vehicle.
https://www.ebay.com/itm/305345588847?_s...BMjJrYk_Rk
Have any owners with old 80’s riveted bodies ever run into this issue(see photos below)?
Rear sidewalls/corners of the coach where multiple aluminum bows line up. Rivets are damaged or none existent and has cause pretty large gap that can even be seen on the inside.
Any advice would be appreciated, I don’t really know where to start with this one. Thank you!
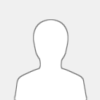
Ok I’m starting another thread about my air system saga that is hopefully less convoluted. First off I got my 120v compressor back on line. It was two separate problems. One, the one way check valve was bad and two… the unloaded solenoid was bad. It is working now (aside from occasionally blowing the 20 amp breaker). My coach has a raised bed slide on the drivers side and a dropping floor slide on the passenger side. Both slides have vacuum systems added to the regulators and two way valves in the lower compartment that switched between regulated pressurized air to fill the seals and vacuum to deflate them. I found one (drivers side - same as was having loud seal leak before ) had a vacuum pump that was blown apart. During trouble shooting the system , I found a piece of teflon tape stuck in the 2 way Parker valve not allowing the valve to completely close in either direction. The valve was open to the vacuum pump during pressurizing the seal and it caused the pump to blow apart. I repaired the valve and the replace the pump and thought all was well…. Until this morning. We spent the night in Reno on our way to California for a late thanksgiving. Woke up this morning and fire up the 60. After few seconds I started to hear air hissing inside the coach. It was coming from under the head board ( just like before). I ran outside and heard air hissing from the seal regulator (drivers side again) in the lower compartment an the passengers side. The regulator was venting heavily, but the pressure read 70 psi. I ran over to the drivers side seal and heard the air hissing (yes over the sound of the engine). I ran back inside and shut the engine off and stabbed the brake several times. The hissing from the rear finally stopped. ( I also learned my low air alarm is not working.) Anyway after I bled the system down with the brake I fired it up again and all was fine???? What the heck. It was below freezing so wondering is some check valve may have froze up. I’m totally confused!!! Any ideas?
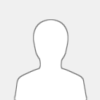
If you have an issue with the dash A/C fan only working on High, I found a cross reference for the resistor(there are two if you have passenger controls also).
Motorcraft D8BH19A706AB or D8BZ19A706A for a 1979 to 1981 Ford Mustang
I have attached a picture of the back side which shows the plug configuration. I am sure there are more cross-references out there, but I have verified this works. Setting 1 and 2 may be the same speed(hard to tell), but 2-4 definitely increase blower speed. I have tested this for a couple of trips and everything is working great.
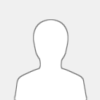
Hello,
My name is Mick.
Newell Coach #1612
45' side entry
I will be looking for help soonnregarding some minor issues with auxilary air systems.
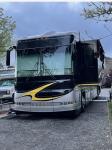
Just purchased 2006 Nuwell it has ZF transmission with the problem. Anybody can suggest where I can find the remedy, the transmission stuck on manual mod and doesn't wan shift to automati.
This forum has been the greatest resource I can imagine for owning a Newell. However, I have to admit I cannot figure out the search engine. I posted two screenshots of my search inquiry and my return. None of the returns had anything to do with my search. Can anybody give me a hand and tell me what I am doing wrong…. Oh, and if someone wants to pipe up on the proper gear lube for the tag axles, that would be great too!
My radio cant be heard when the generator is running. It is on and all functions are operable but nothing comes from speakers. However it can be heard when generator is off and coach is running. Any suggestions as to why? Thanks